Dalla valutazione della qualità all'ottimizzazione dei processi

Qualche settimana fa, Holzbau Gröber ha ordinato a MiCROTEC il millesimo scanner per schede di qualità Goldeneye. Il CSO Arianna Giudiceandrea e il CEO Frank Jöst hanno colto questa pietra miliare come un'opportunità per guardare indietro ai risultati ottenuti da MiCROTEC fino ad oggi. Pur apprezzando oltremodo tutti i risultati ottenuti in passato, i due si concentrano soprattutto sulle sfide presenti e future dell'azienda e sulla tecnologia degli scanner.
L'articolo completo di TIMBER-ONLINE è disponibile qui.
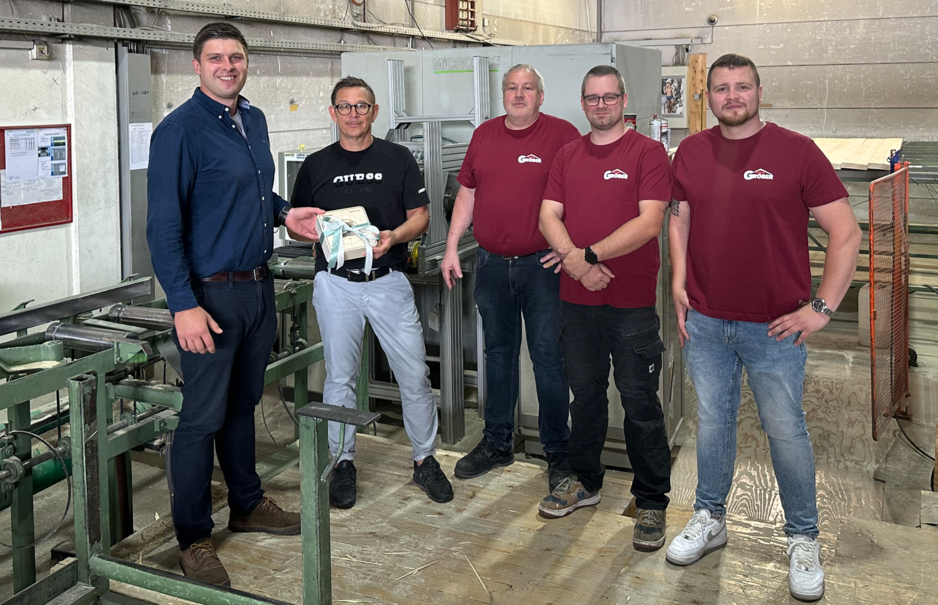
Intelligent operator
Today, the Goldeneye is a multi-sensor quality scanner which combines scattering lasers, 3D lasers, color, and X-ray to assure the highest precision grading and classification of softwood lumber. The focus is on strength grading and on lumber for construction purposes and outdoor use. The Goldeneye’s counterpart for hardwood lumber is the Woodeye, complete with optimization software, which is used to detect aesthetic and/or quality defects in the wood, depending on the specified requirements.
In recent years, the sawmill industry has gone from doing manual quality assessment to relying on scanners. For a long time, companies always had an in-house specialist who operated the scanner. “Since it has become increasingly difficult for customers to find such experts, we have developed the digital quality control tool QC Assist, which provides important support when adjusting the Goldeneye,” Giudiceandrea tells us and adds: “Our Goldeneye scanners always start off with the highest performance. However, if target specifications change or the quality of the lumber fluctuates above average, the scanner needs to be adjusted. Today, our QC Assist supports the operator. In the future, though, an AI solution will turn the scanner itself into an intelligent operator.”
From lumber to log wood
Then as now, strength grading is the core task of the Goldeneye, and MiCROTEC constantly works on increasing both quality and speed. “Ours are the fastest scanners on the market, and we are also working tirelessly on increasing yield. In addition, our systems are also taking on more and more optimization tasks along the entire production process,” Jöst explains.
For a long time, MiCROTEC scanners were only used for assessing dried boards, but the systems have evolved towards log wood via wet sorting. “With several scanners along the entire production process, our scanner systems no longer just assess the end result. Now, they can intervene in the process even before the first cut,” Giudiceandrea explains, referring in particular to the CT Log scanner. This scanner divides each log into virtual boards, which can significantly improve the yield and warehousing of a sawmill by making it possible to cut on demand.
“If several of our scanners are in use, we can use a fingerprint solution to precisely track the path from the board to the log or in the opposite direction, incorporate cross-learnings and further optimize the process in numerous places, thereby relieving the burden on staff. All processes are increasingly supported by AI solutions, which will play a central role in the future,” Jöst says. He assumes that stand-alone scanner systems will only be of interest for few applications in the future.
The full article from TIMBER-ONLINE can be found here.
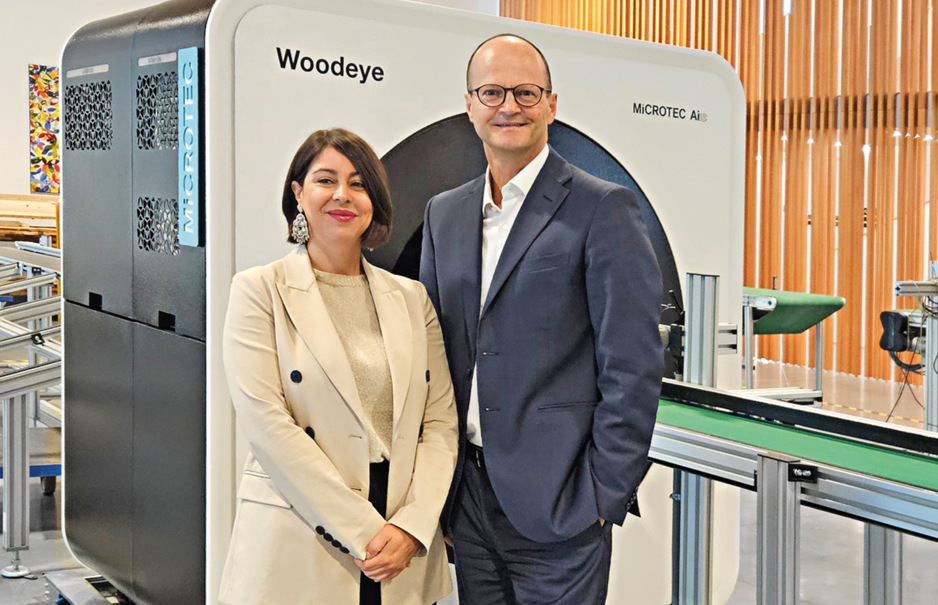